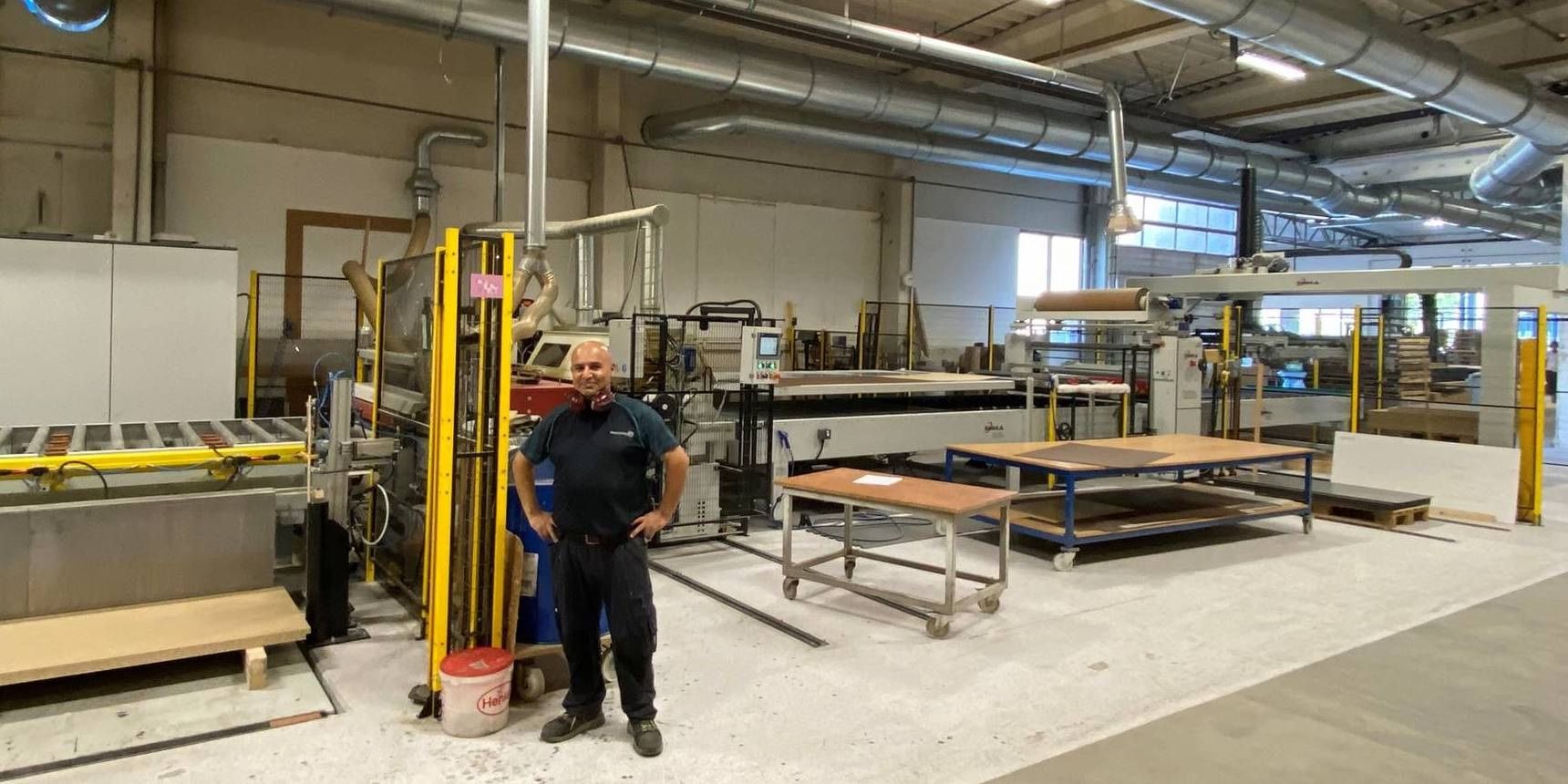
Crecer de forma sostenible gracias al pensamiento Lean
La historia del fabricante de muebles noruego Haugstad Møbel que, gracias al pensamiento Lean, pudo transformar su cultura y desbloquear el potencial del crecimiento sostenible.
En 2016, Haugstad Møbel era un pequeño productor de muebles de madera. Si entrabas a la fábrica, no había cambiado mucho en los últimos 30 años. Habían pasado 70 años desde que se fundó la empresa. En ese momento, los propietarios vieron potencial en los productos que fabricaban y rápidamente decidieron trasladar la fábrica a unas nuevas instalaciones. En 1963 se construyeron e inauguraron una nueva fábrica y se realizaron inversiones en equipos de mecanizado modernos hasta 1989. Después todo se calmó y el volumen de negocios se mantuvo más o menos igual durante 30 años.
Siempre hubo una cultura "monozukuri" en toda la empresa. Tanto es así que cuando Steinar Gulaker asumió el cargo de director general en 2015, se esperaba que eligiera una máquina propia y se dedicara a la producción. Sin embargo, monozukuri sin hitozukuri (la pasión por crear personas) deja a la empresa estancada. Y Steinar sabía que Haugstad necesitaba seguir adelante. Su misión era aprovechar la pasión por hacer cosas, inculcar la pasión por desarrollar a las personas y crear una cultura de "Kotozukuri", la pasión por hacer que las cosas sucedan. Y estaban a punto de suceder cosas.
En 2017, Haugstad Møbel se embarcó en el primero de tres proyectos de investigación con SINTEF Manufacturing, financiado por el Consejo Noruego de Investigación. El proyecto inicial exploró la posibilidad de integrar la tecnología digital en equipos de producción antiguos. Le brindó a Steinar la oportunidad de estudiar fábricas modernizadas en toda Europa que producían productos similares a los de Haugstad. Lo que observó le hizo darse cuenta de que no eran los salarios los que impedían que las empresas noruegas compitieran. Haugstad estaba décadas por detrás de las mejores empresas de Europa en lo que respecta a la aplicación tanto de tecnología de producción moderna como de principios de producción Lean.
Hacer las cosas más fáciles
Haugstad tenía una antigua célula de producción manual para pegar y prensar laminado sobre tablas de madera, que luego se cortaban para fabricar piezas para el producto terminado. La célula constaba de cuatro máquinas y requería cuatro operarios para producir cien planchas al día. Dado el trabajo pesado que implicaba, muchos operarios tenían problemas con su salud física. Cuando Steinar sugirió utilizar esta línea como ejemplo de cómo se podrían mejorar tanto la productividad como las condiciones de producción, el equipo no se mostró demasiado entusiasmado. Sin embargo, una vez instalada la nueva línea, nadie quiso volver a la antigua forma de trabajar.
La nueva línea estaba completamente automatizada, con todos los procesos perfectamente acoplados en un flujo de una sola pieza, eliminando la necesidad de levantar objetos pesados. Ahora, un solo operario podría manejar toda la línea y producir 110 planchas por hora. A pesar del escepticismo inicial sobre este nuevo y moderno enfoque de fabricación, se estaba desarrollando una transformación. Y eso fue solo el principio.
Una fábrica moderna
Las visitas a los competidores europeos fueron reveladoras para los altos directivos de Haugstad. Recorrer fábricas modernas equipadas con sistemas de producción contemporáneos diseñados tanto para el flujo como para la flexibilidad les hizo darse cuenta de que sus equipos obsoletos, mal mantenidos durante muchos años, les dejaban pocas posibilidades de progresar. El ideal Lean es, por supuesto, comenzar con lo que se tiene, hacerlo funcionar y asegurarse de que fluya a través de la resolución de problemas. Sin embargo, como dice la historia del sensei: “TPS bueno. A veces: sea flexible”. Y en el caso de Haugstad, la mayor parte del equipo antiguo no podía repararse y se necesitaba inversión.
Afortunadamente, los propietarios y su banco vieron una oportunidad en Haugstad. Estuvieron presentes personas apasionadas que realmente se preocupaban por su trabajo y la empresa. Por lo tanto, se aprobó la inversión necesaria en equipos de producción modernos e integrados digitalmente para hacer crecer la empresa. Lo que Haugstad pronto descubrió fue que las soluciones completamente nuevas conllevan problemas completamente nuevos, y el camino desde el diseño de las nuevas líneas de producción hasta su puesta en funcionamiento según lo previsto resultó ser largo y sinuoso.
Primero, llegó el Covid y los plazos de entrega de muchas de las máquinas de repente se volvieron mucho más largos de lo previsto inicialmente. Se suponía que la primera prueba se realizaría en octubre de 2020, pero se necesitaron otros ocho meses para enviar suficientes equipos de producción a Noruega y prepararlos para las pruebas. A finales de 2022, solo una de cada tres nuevas líneas de producción estaba en pleno funcionamiento y se necesitarían algunos meses más para poner en funcionamiento las otras dos. De hecho, Haugstad todavía está esperando que llegue una de las nuevas máquinas, pero el fabricante les prestó una similar de forma gratuita. Finalmente, en el verano de 2023, tres años después de la primera prueba prevista, las nuevas líneas de producción finalmente estaban en funcionamiento. En el proceso de implementación del nuevo equipo, Haugstad descubrió que las cosas nuevas no cambian los viejos hábitos, y la capacidad de los nuevos equipos es inútil a menos que también se desarrolle a las personas, el mercado y se arregle la logística y la distribución internas.
La visita del sensei
En otoño de 2021, Steinar invitó al sensei Michael Ballé a visitar la fábrica durante su viaje por carretera por Noruega. Anteriormente había bromeado con Steinar y Olav (su planificador de producción), diciéndoles que, para ser dos tipos que decían que no les gustaba poner cosas en pallets, seguramente tenían muchas cosas y muchos pallets por ahí. Después del gemba walk, Steinar le preguntó a Michael qué pensaba sobre el nuevo equipo de producción, pero Michael no estaba particularmente interesado en eso. El papel del sensei es ayudar a los directores ejecutivos a encontrar y enfrentarse a sus problemas reales, y Michael identificó que la principal preocupación no era el nuevo equipo de producción, sino la logística, algo que Steinar necesitaba abordar.
Como primer paso, Michael sugirió que Steinar separara completamente la logística de la producción para aclarar el desorden. Durante la visita, piezas y pallets se encontraban esparcidos por todos lados, prevaleciendo el lema “si encuentras un lugar libre, ponlo ahí”. El resultado fue una fábrica desorganizada con operarios moviéndose constantemente de un lado a otro para localizar piezas.
Siguiendo el consejo de Michael, Steinar tomó medidas inmediatas para separar la logística y la producción. El gemba walk tuvo lugar un martes y, para el fin de semana, Steinar y algunos otros habían trasladado todas las piezas a un área designada destinada a servir como departamento de logística interna de la fábrica. En el proceso, también trasladaron las estaciones de montaje manual a la nueva fábrica, estableciendo un área de montaje entre la línea de producción y el área de distribución. Steinar reorganizó además la fábrica en tres funciones distintas: logística, producción y distribución, con relaciones proveedor/cliente claramente definidas entre las funciones. Este paso fue solo el comienzo de un viaje que permitió a Haugstad aprovechar todo el potencial de sus inversiones.
De procesos Lean a una estrategia Lean
Steinar ya estaba intentando desarrollar procesos eficientes, crear flujo e implementar las 5S, pero el gran avance se produjo después de la visita del sensei. Cuando Steinar comenzó su viaje con Haugstad, su marco estratégico se basó en el tradicional 4D: Definir, Decidir, Drive (Impulsar), Deal (Negociar). Sin embargo, después de trabajar con dos sensei lean diferentes, se dio cuenta de la necesidad de cambiar su enfoque. Las inversiones realizadas fueron necesarias e inteligentes, pero se requirió una estrategia diferente para aprovechar todo su potencial. El marco 4F de la estrategia Lean proporcionó a Steinar un modelo de pensamiento perfecto para avanzar, uno que se basa en aceptar desafíos y comprometerse con el cambio al involucrar a todos en la organización en la creación de nuevas formas de trabajar.
Para Steinar y Haugstad, el Sistema de Producción Toyota se convirtió en el modelo de referencia, actuando como un sistema educativo para desarrollar personas y procesos simultáneamente. En un gemba walk tras otro, Steinar y su sensei interactuaban con operarios y líderes de equipo, señalando áreas donde el proceso no estaba funcionando como debería y brindando herramientas de resolución de problemas para capacitar a las personas de primera línea para que formen sus propias soluciones. A medida que las cosas avanzaban y los problemas se resolvían, subieron el listón.
En el taller de CNC, una de las dos células de producción restantes que no están conectadas directamente a las líneas de producción principales, el equipo tuvo problemas para hacer frente a una acumulación de pedidos de tres semanas y no pudo ver una manera de resolver este problema. Las ventas estaban aumentando, por lo que reducir la carga de la célula no era una opción. Anteriormente, una importante discusión en la gestión diaria de la Obeya había convencido a Olav, el planificador de producción, de pasar de la programación semanal a la programación diaria de las cocinas. El efecto fue extraordinario, ya que ayudó a todos en el proceso de producción a tomar mejores decisiones en cada paso y evitar suboptimizar sus propios procesos.
Mientras se discutían y celebraban los resultados de este cambio, el sensei mencionó que el objetivo debería ser la programación horaria, lo que indica que todavía quedaba un largo camino por recorrer. Al final, esta se convirtió en la llave que abrió el taller de CNC. Después de una discusión con el equipo de CNC, Olav, Steinar y el equipo establecieron un objetivo de producción por horas y gradualmente (primero lentamente y luego rápidamente) lograron eliminar el retraso.
Con una capacidad aumentada de 2.000 piezas por semana a 2.300 piezas por día, el número de pedidos enviados también se ha quintuplicado. Una vez más, visualizar el flujo de información con mayor precisión ha demostrado ser fundamental para ayudar al equipo de distribución a encontrar una manera de gestionar el aumento de pedidos sin acumular grandes cantidades de inventario. El mismo enfoque ha ayudado al equipo de montaje a alinearse con su cliente intermedio, contribuyendo a una mejor alineación y coordinación general en toda la fábrica.
Pasos hacia atrás y hacia adelante: arreglar el equipo
Como todas las transformaciones lean, el viaje de Haugstad ha estado lleno de altibajos. Una idea clave del CEO Lean de Aramis Auto, Nicolas Chartier, es que el primer paso de cualquier transformación Lean es arreglar el equipo. Implica ofrecer a las personas el tipo de trabajo adecuado, identificar a aquellos que están entusiasmados con kaizen, desarrollar líderes de equipo altamente capacitados y trasladar a aquellos que no tienen lo necesario para trabajar en una organización que quiere cambiarse a sí misma. Este desafío se hizo evidente para Steinar con el paso del tiempo. Junto con su sensei, invirtió en personas que creía que tenían las cualidades necesarias pero, la mayoría de las veces, terminaban decepcionadas.
El papel de director de producción resultó ser particularmente difícil de desempeñar, ya que la vieja idea de optimizar cada paso de la producción instruyendo a todos y tratando de controlar el resultado estaba profundamente arraigada. Después de varios intentos fallidos, Steinar finalmente encontró a la persona adecuada en Olav, el planificador de producción. Desarrollar un tema estratégico para encontrar el trabajo adecuado para diferentes empleados en Haugstad surgió como un medio para evitar retrocesos y contrarrestar retrocesos, y Steinar parecía tener una habilidad especial para ello. Un ex operario de CNC que inicialmente no aceptó la idea de que el siguiente proceso es su cliente, ahora se destaca en programación.
No dejes de creer (no sueltes ese sentimiento)
No es muy frecuente encontrar una empresa de fabricación del tamaño de Haugstad Møbel que invierta en el futuro como lo hacen ellos. Además de cuatro personas que trabajan a tiempo completo en la digitalización, dos diseñadores de productos son responsables del desarrollo de la próxima generación de muebles sostenibles. Sin embargo, Haugstad no se centra únicamente en el futuro de sus propios productos y procesos. A solo 20 minutos en auto de la fábrica principal, han establecido un Hub Circular, una fábrica de aprendizaje donde niños de 14 a 15 años aprenden sobre la economía circular creando sus propias empresas emergentes, productos y modelos de negocios circulares. Además de servir como fábrica de aprendizaje, el Hub Circular también funciona como instalación de reventa, reacondicionamiento y reutilización, dando nueva vida a productos antiguos, algunos de los cuales no se han utilizado y aún se encuentran en su embalaje original.
Para los profesionales lean, este es el futuro. Ya no basta con mejorar el modelo de negocio lineal. Para afrontar la crisis medioambiental, debemos emplear nuestras habilidades colectivas lean para desarrollar y mejorar modelos de negocio circulares nuevos e innovadores. Esto implica aprovechar el marco 4F de Lean como una alternativa al 4D tradicional, desafiando y apoyando, en lugar de instruir y controlar. Luego, a través de yokoten, nuestro enfoque distintivo para compartir conocimientos y aprender, tenemos la oportunidad y la responsabilidad únicas de contribuir a un futuro sostenible, tanto a nivel local como global. Dejemos que empresas como Haugstad Møbel nos inspiren a ser el cambio que queremos ver en el mundo.
Eivind Reke Secretario de organización en Los Norge y coautor de El sensei LeanExtraído de: Planet Lean